Comprehensive Guide: What is Porosity in Welding and Just How to avoid It
Recognizing Porosity in Welding: Exploring Causes, Results, and Avoidance Techniques
As professionals in the welding market are well mindful, comprehending the causes, impacts, and prevention strategies associated to porosity is vital for attaining durable and dependable welds. By delving right into the origin causes of porosity, examining its damaging results on weld quality, and checking out effective avoidance techniques, welders can enhance their expertise and abilities to generate high-quality welds constantly.
Common Reasons For Porosity
Contamination, in the kind of dirt, oil, or corrosion on the welding surface area, produces gas pockets when heated, leading to porosity in the weld. Improper securing occurs when the securing gas, commonly used in procedures like MIG and TIG welding, is unable to completely secure the molten weld pool from responding with the bordering air, resulting in gas entrapment and succeeding porosity. Furthermore, poor gas coverage, often due to incorrect flow rates or nozzle positioning, can leave components of the weld unprotected, enabling porosity to form.
Results on Weld Quality
The visibility of porosity in a weld can considerably compromise the total quality and integrity of the bonded joint. Porosity within a weld produces voids or dental caries that damage the framework, making it a lot more prone to cracking, rust, and mechanical failing. These spaces act as anxiety concentrators, decreasing the load-bearing capacity of the weld and enhancing the possibility of early failing under applied stress and anxiety. On top of that, porosity can additionally function as possible sites for hydrogen entrapment, further aggravating the degradation of the weld's mechanical residential or commercial properties.
Furthermore, porosity can impede the effectiveness of non-destructive testing (NDT) strategies, making it challenging to spot other flaws or discontinuities within the weld. This can bring about significant safety worries, especially in vital applications where the architectural stability of the bonded elements is critical.
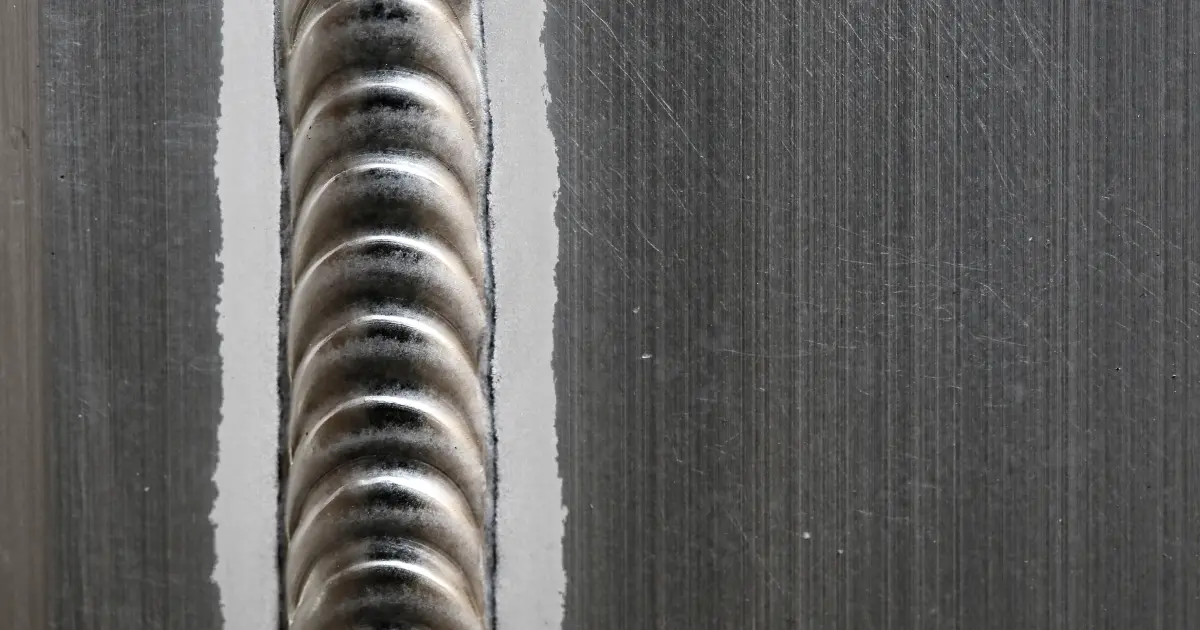
Prevention Techniques Summary
Provided the damaging impact of porosity on weld quality, efficient prevention techniques are crucial to preserving the architectural honesty of bonded joints. In addition, choosing the proper welding parameters, such as voltage, current, and take a trip rate, can aid reduce the threat of porosity formation. By integrating these avoidance strategies into welding techniques, the incident of porosity can be considerably decreased, leading to stronger and a lot more reputable bonded joints.
Significance of Proper Shielding
Correct protecting in welding plays an essential duty in stopping atmospheric contamination and making certain the integrity of welded joints. Protecting gases, such as argon, helium, or a combination of both, are typically used to secure the weld pool from reacting with aspects airborne like oxygen and nitrogen. When these reactive elements come into call with the warm weld swimming pool, they can create porosity, resulting in weak welds with decreased mechanical homes.

Insufficient securing can lead to numerous problems like porosity, spatter, and oxidation, jeopardizing the architectural integrity of the welded joint. Therefore, sticking to correct shielding practices is important to create top quality welds with very little problems and make certain the longevity and reliability of the welded parts (What is Porosity).
Tracking and Control Techniques
Just how can welders effectively check and manage the welding procedure to guarantee optimum results and stop issues like porosity? By continually keeping an eye on these variables, from this source welders can recognize inconsistencies from the perfect conditions and make prompt changes to stop porosity development.

Additionally, carrying out correct training programs for welders is crucial for keeping track of and regulating the welding process effectively. What is Porosity. Educating welders on the significance of keeping constant specifications, such as proper gas protecting and take a trip speed, can aid prevent porosity problems. Routine assessments and qualifications can likewise make certain that welders are efficient in monitoring and managing welding procedures
Additionally, the usage of automated welding systems can boost monitoring and control capacities. These systems can precisely regulate welding parameters, minimizing the possibility of human mistake and guaranteeing consistent weld high quality. By integrating advanced monitoring technologies, training programs, and automated systems, welders can successfully check and regulate the welding process to lessen porosity problems and attain premium welds.
Verdict
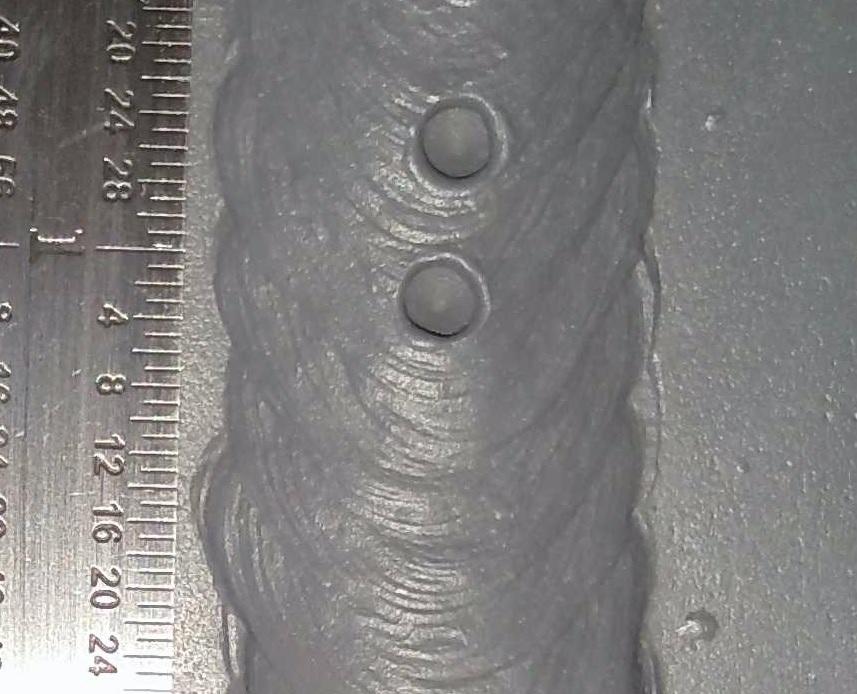